As a qualified cosmetics product manager, it is essential to understand various packaging processes.
Packaging processes can be roughly divided into 2 categories: the printing process and colouring process.
In this post, I will share 6 common printing processes for cosmetic inner packaging.
- Silk-screen printing
- Hot stamping
- Water transfer printing
- Thermal-transfer printing
- Offset printing
- 3D relief UV printing
Next, I would like to provide a brief introduction to these six processes.
The first one is silk screen printing, favoured for its versatility, durability, and ability to produce vibrant colours. It is widely used in the fashion industry, promotional products, and art prints.
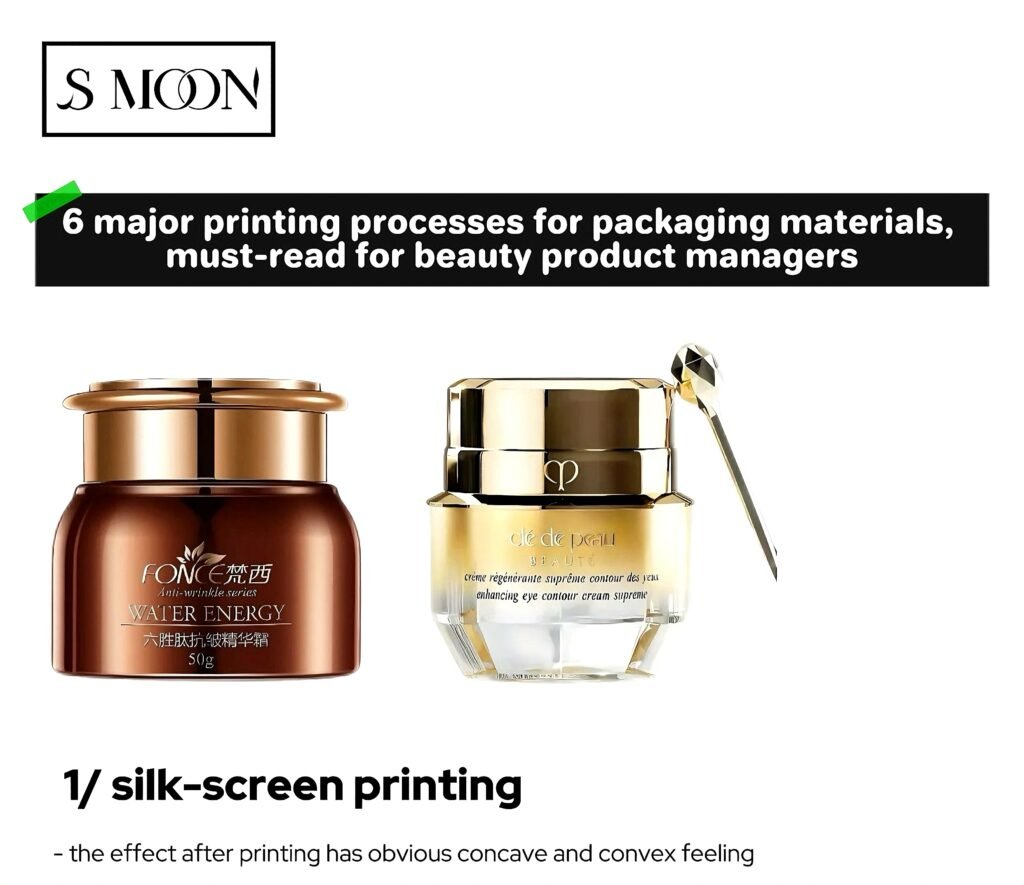
1/ Silk-screen printing: the effect after printing has an obvious concave and convex feeling.
Factors that affect the price of silk screen printing:
01. Silk screen printing area:
Silkscreen regular bottles (cylindrical) can be printed at one time irregular bottles are charged according to different areas
02. The number of silkscreen colours.
03. Types of silk screen printing ink: self-drying ink and UV ink. Self-drying ink is easy to fade over time and can be wiped off with alcohol; UV ink has an obvious concave and convex feeling to the touch and is difficult to wipe off
Hot stamping, also known as hot foil stamping, is a versatile printing technique widely used in various industries to create eye-catching, high-quality prints. This process involves transferring metallic or pigmented foil onto paper or cardstock using heat and pressure, resulting in a striking finish that enhances the aesthetic appeal of products like packaging, labels, and decorative items.
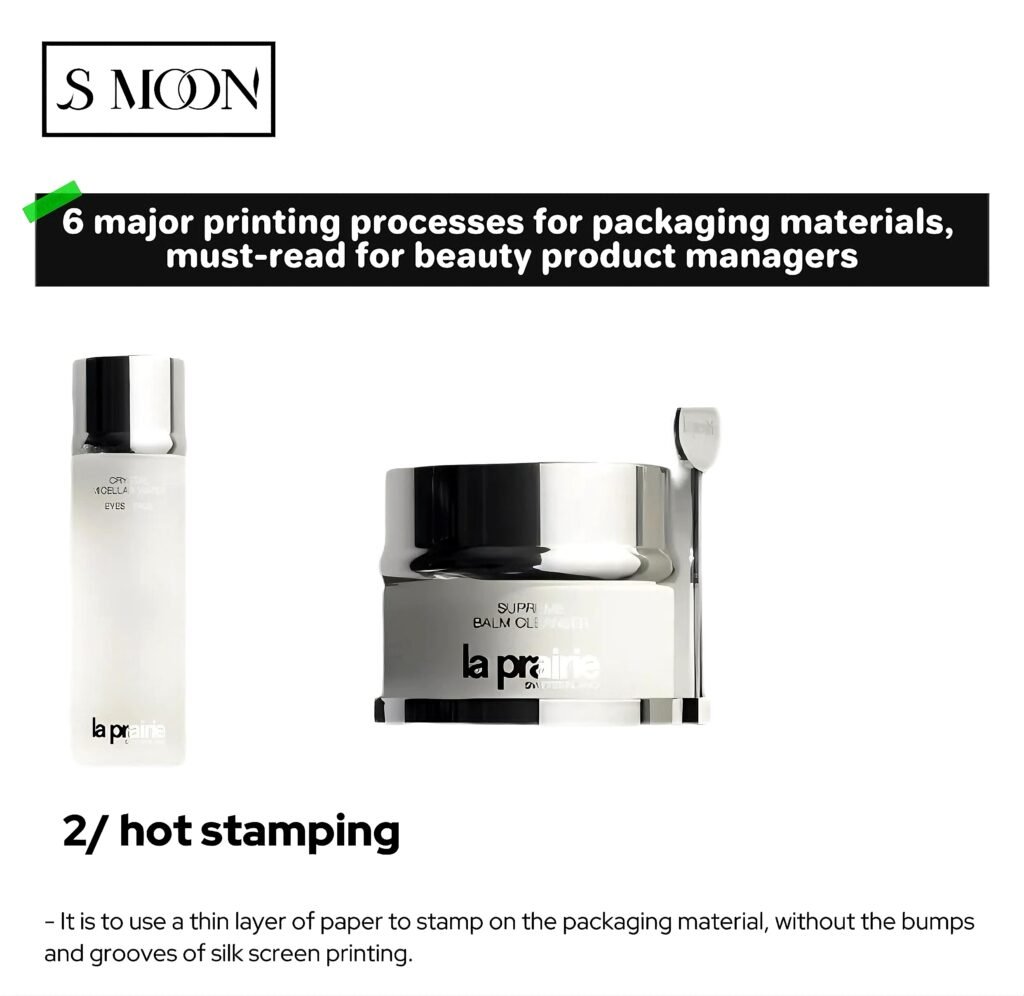
2/ Hot stamping: It uses a thin layer of paper to stamp on the packaging material, without the bumps and grooves of silk screen printing.
Hot stamping is not recommended to be used directly on PE and PP materials. It is necessary to perform heat transfer first and then hot stamping. If there is good hot-stamping paper, it can be hot-stamped directly.
Hot stamping cannot be done on aluminium-plastic but it can be done on full plastic
Water transfer printing, also known as hydro dipping or hydrographic printing, is a method of applying printed designs to three-dimensional surfaces such as metal, plastic, glass, and wood.
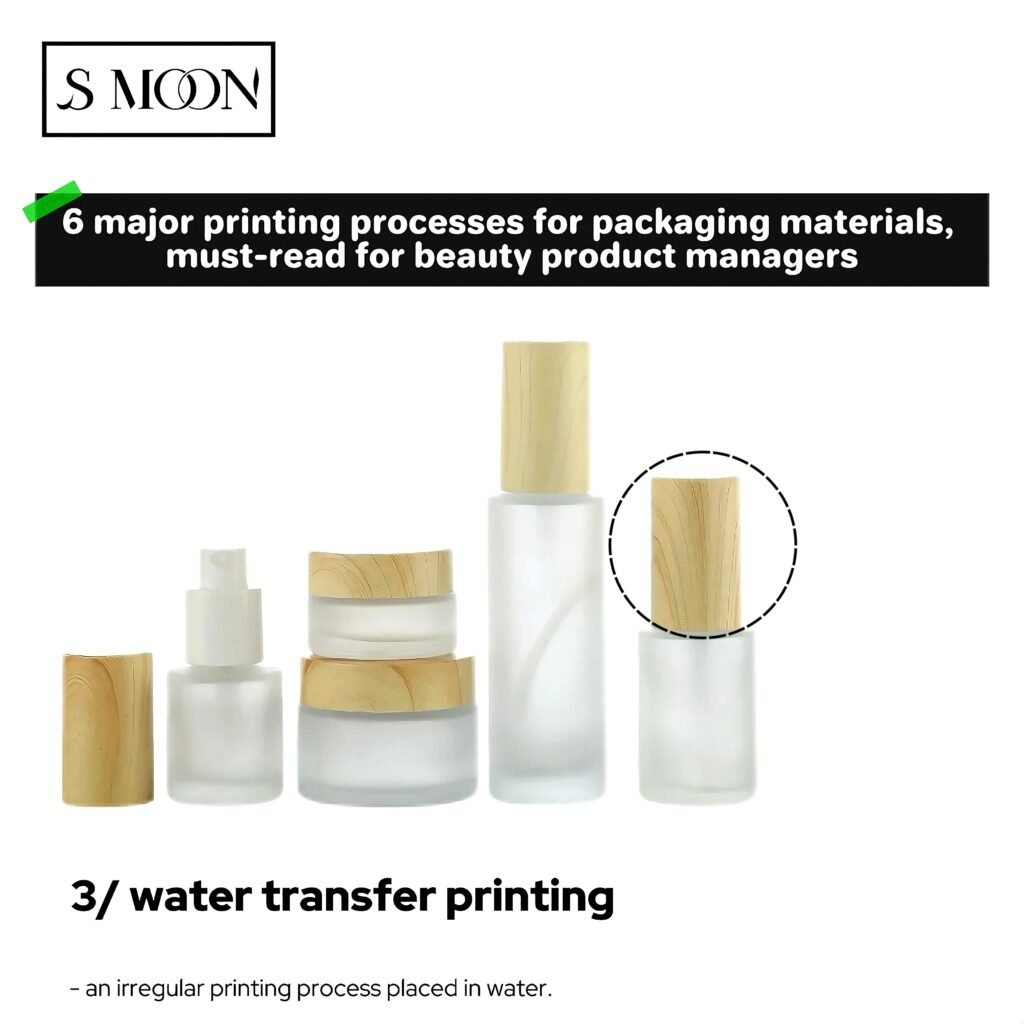
3/ Water transfer printing: an irregular printing process placed in water.
The printed texture is inconsistent and the price is more expensive.
Thermal-transfer printing is a digital printing method where material is applied to paper by melting a ribbon coating to adhere it to the material. It is different from direct thermal printing, which does not use a ribbon.
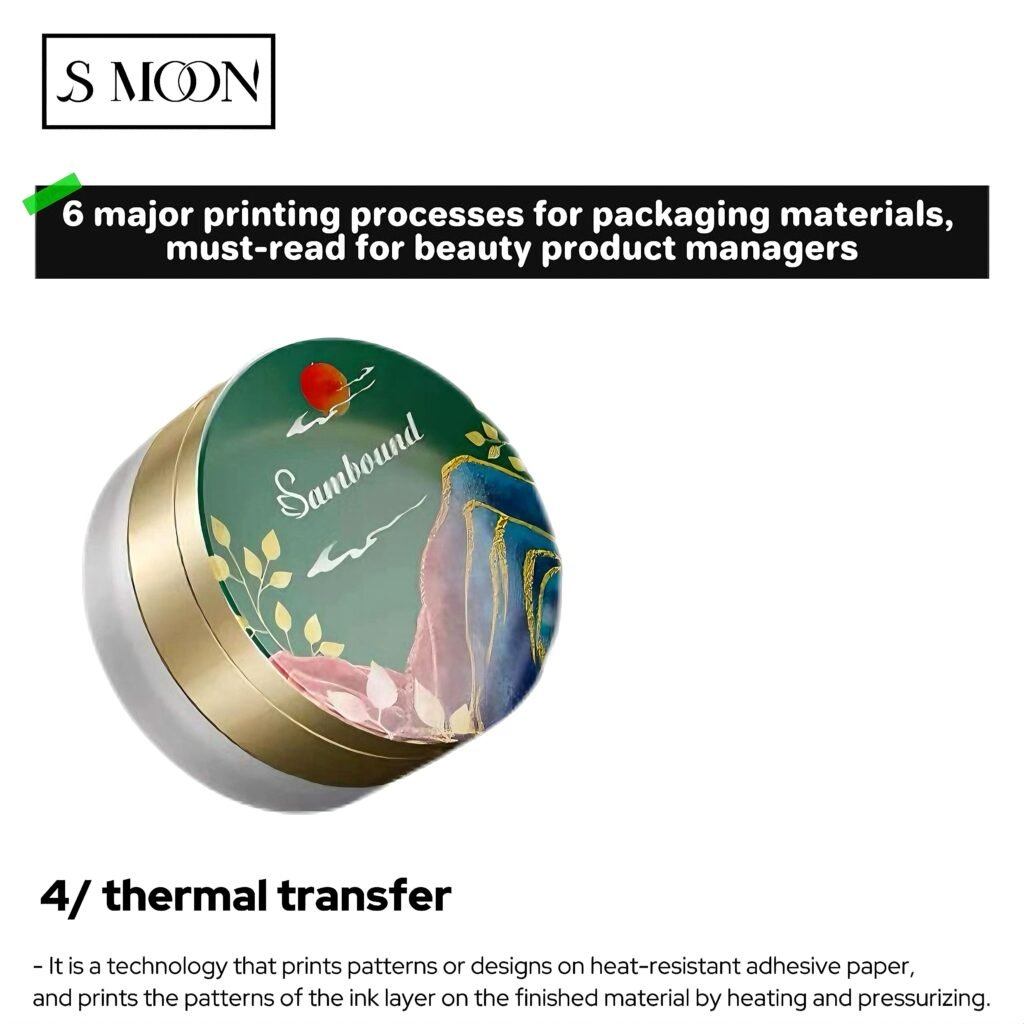
4/ Thermal-transfer printing: lt is a technology that prints patterns or designs on heat-resistant adhesive paper, and prints the patterns of the ink layer on the finished material by heating and pressurizing.
Using thermal transfer film printing, multi-colour patterns can be printed at one time. without colour matching, and simple equipment can also print realistic patterns.
Thermal transfer is mostly used for large-volume and complex printing products,and the price is relatively expensive.
Offset printing is a popular method where the inked image is transferred from a plate to a rubber blanket and then to the printing surface. This technique works with the lithographic process, which is based on the repulsion of oil and water. In offset printing, a flat (planographic) image carrier is used. Ink rollers apply ink to the image areas, while a water roller applies a water-based film to the non-image areas.
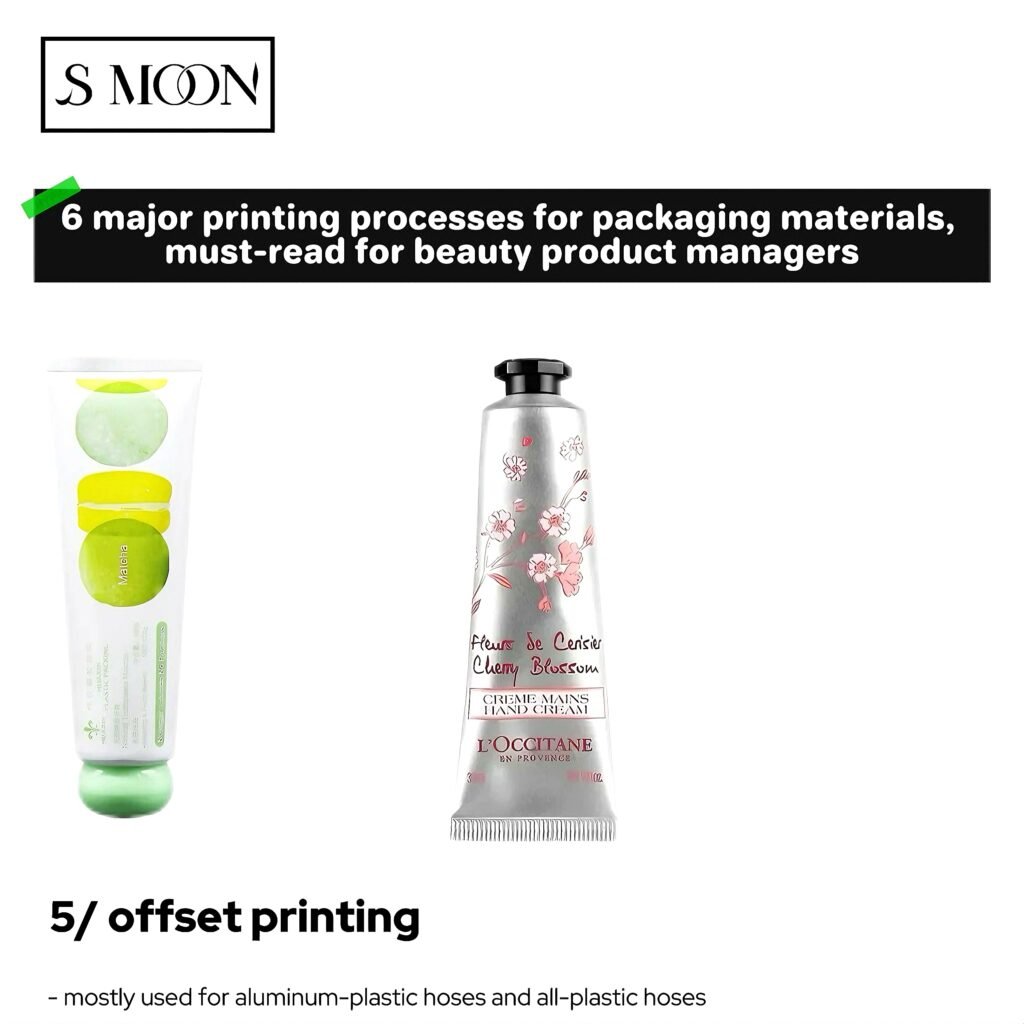
5/ Offset printing: mostly used for aluminum-plastic hoses and all-plastic hoses.
When printing white on coloured hoses, screen printing must be used, because offset printing will cause the base colour to show through, affecting the effect.
Sometimes a layer of glossy film or semi-film is added to the surface of the hose to enhance the appearance and protect the printed pattern.
3D relief UV printing is a specialized technique that creates tactile and visually striking designs on surfaces using UV light to cure ink and produce raised textures and effects.
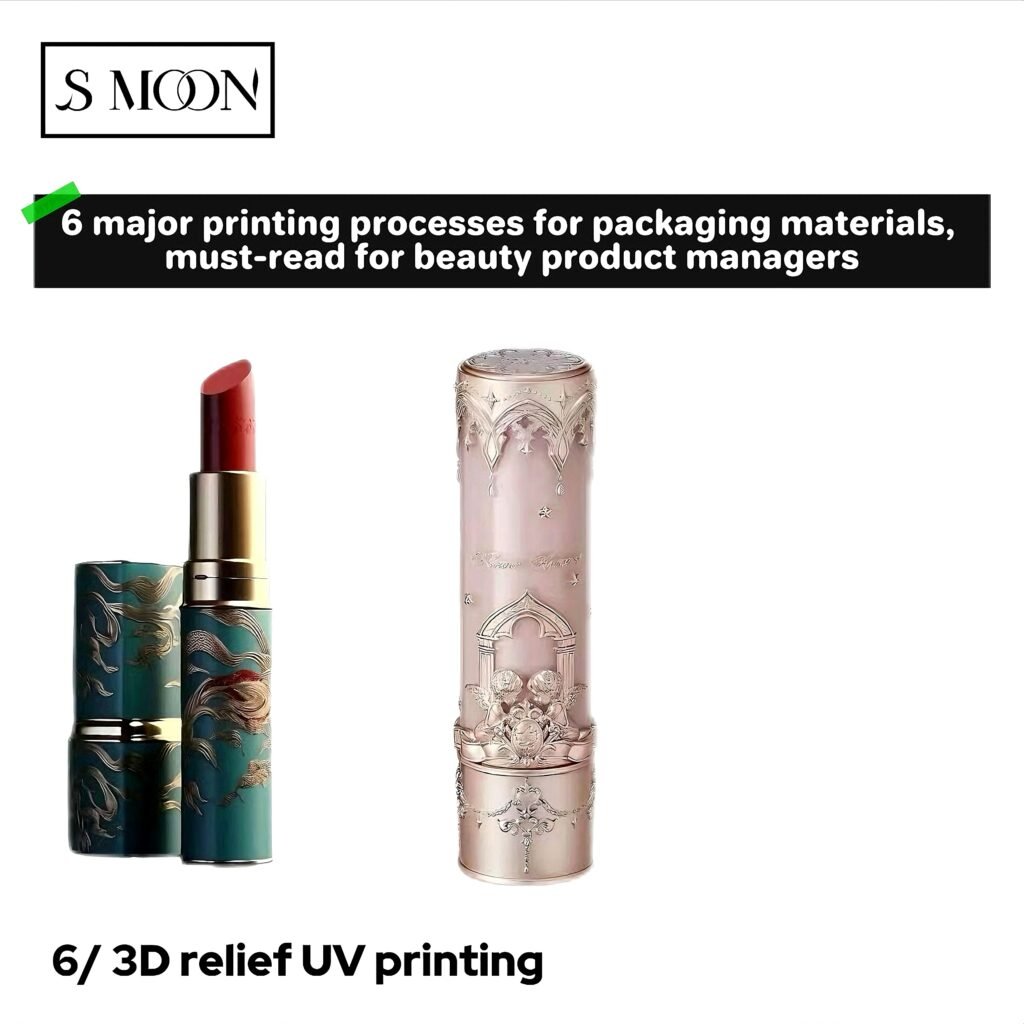
6/ 3D relief UV printing : 3-layer printing function: white, color, and varnish, can be performed at once.
When printing on any medium, pre-process with white ink that can reproduce colour reproduction, and add another layer of varnish on the surface to obtain a more beautiful printing effect.
The 6 common packaging printing processes above can be flexibly used by product packaging designers for different products. If you have a project that requires glass packaging products, please contact us. Thank you!